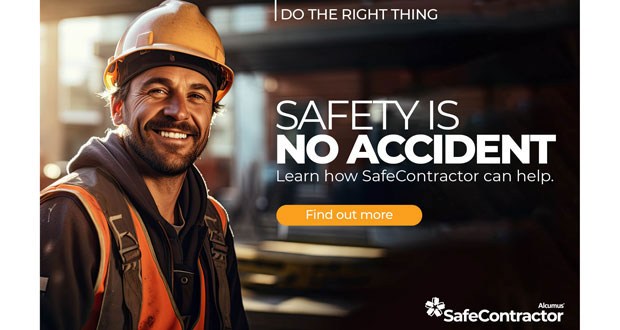
Learn how SafeContractor can help: https://lp.safecontractor.com/safety-is-no-accident
Today’s complex supply chains rely heavily on onsite contractors, each playing a pivotal role in your business. The effective management of these contractors is vital, however the challenge lies in how to source and manage them without compromising on safety, sustainability, or ethics.
Despite health and safety being a legal obligation and at the forefront of most contractor management processes, there is an alarming rise in workplace injuries and fatalities. The HSE statistics for 2021/2022 reveal a sobering reality – 135 workers sustained fatal injuries last year, a stark increase from 123 the previous year.
Additionally, a staggering 565,000 workers sustained non-fatal injuries, resulting in the loss of 6 million working days. To compound the issue, the independent analyst group, Verdantix, highlights that recordable safety incident rates are typically three times higher for contractors compared with permanent staff.
A breach in health and safety standards can be devastating, and it’s worth noting the average health and safety fine has also risen to an all-time high of £150,000.
So, what does this mean for you? Dale Jones emphasises: “The guidance for the Construction (Design and Management) Regulations (CDM) is quite clear. Anyone appointing a contractor needs to take reasonable steps to ensure that the contractor has the skills, knowledge, experience, and organisational capability to carry out the work safely.”
This means when using onsite contractors for their projects, businesses need to assure themselves that they have:
- Clear visibility of the risk profile of all onsite contractors within the supply chain
- Evidence that onsite contractors meet minimum industry best practice standards and, where applicable, comply with the relevant regulatory and legal requirements
- Ongoing monitoring of the health and safety credentials of onsite contractors
- Regular assessments of the operational, ethical, and financial risk of onsite contractors
Dynamic Risk-Based Assessments:
Businesses now more than ever, need to scrutinise their supply chain and audit their onsite contractors for health and safety as well as other ESG credentials such as modern slavery, sustainability, and financial standing.
In this instance, a robust and dynamic risk-based assessment is essential. It allows you to assess onsite contractors according to their job profile and industry, avoiding a one-size-fits-all approach that may overlook project complexity and associated risks.
Dale Jones advises: “Any assessment process will need to be sensible, proportionate and address the anticipated risks of the potential work activities that would be undertaken. If you are simply asking generic questions as part of your assessment process for all onsite contractors, how would you capture the differences in risk profile between a decorating contractor and an asbestos removal contractor?”
Some further questions to consider, if the Health and Safety Executive were to visit your site today, or if an incident were to occur, would you be able to showcase that you’ve implemented the necessary and reasonable measures to fulfil the duty of ensuring safe work arrangements are in place? Would the information be readily available? Are your onsite contractors only assessed when they are first onboarded, or are they audited annually with records and qualifications kept up to date?
Safety is no accident. You want onside contractors who aren’t a risk. The legal, moral, and financial consequences of getting it wrong can be severe. Alcumus SafeContractor can help you baseline your supply chain compliance data with a dynamic risk-based assessment.
Find out more about its benefits and see it in action here: https://lp.safecontractor.com/safety-is-no-accident
Dale Jones is the Technical Director at Alcumus SafeContractor and has over 20 years’ experience in the world of third-party assessment and supply chain assurance solutions. For more information, visit: www.safecontractor.com/supply-chain-management/