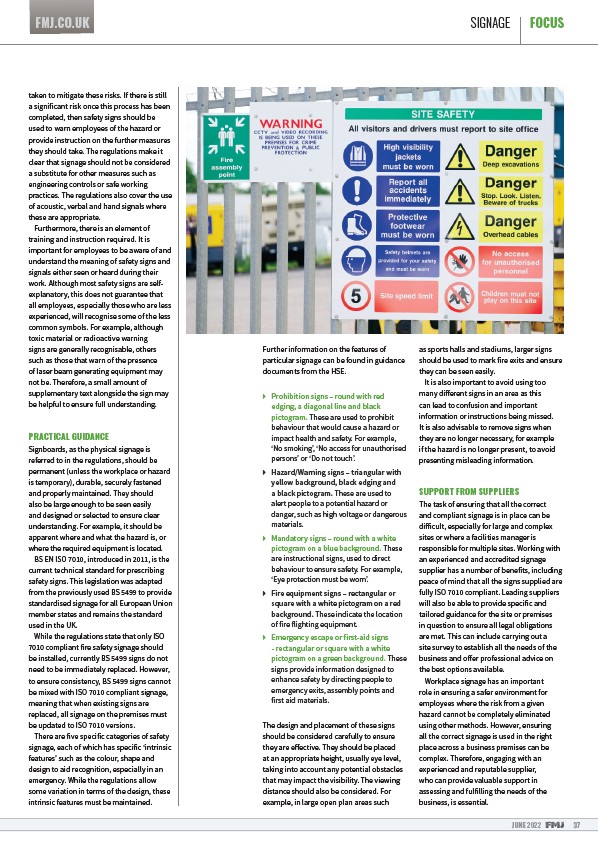
FMJ.CO.UK SIGNAGE FOCUS
JUNE 2022 37
taken to mitigate these risks. If there is still
a significant risk once this process has been
completed, then safety signs should be
used to warn employees of the hazard or
provide instruction on the further measures
they should take. The regulations make it
clear that signage should not be considered
a substitute for other measures such as
engineering controls or safe working
practices. The regulations also cover the use
of acoustic, verbal and hand signals where
these are appropriate.
Furthermore, there is an element of
training and instruction required. It is
important for employees to be aware of and
understand the meaning of safety signs and
signals either seen or heard during their
work. Although most safety signs are selfexplanatory,
this does not guarantee that
all employees, especially those who are less
experienced, will recognise some of the less
common symbols. For example, although
toxic material or radioactive warning
signs are generally recognisable, others
such as those that warn of the presence
of laser beam generating equipment may
not be. Therefore, a small amount of
supplementary text alongside the sign may
be helpful to ensure full understanding.
PRACTICAL GUIDANCE
Signboards, as the physical signage is
referred to in the regulations, should be
permanent (unless the workplace or hazard
is temporary), durable, securely fastened
and properly maintained. They should
also be large enough to be seen easily
and designed or selected to ensure clear
understanding. For example, it should be
apparent where and what the hazard is, or
where the required equipment is located.
BS EN ISO 7010, introduced in 2011, is the
current technical standard for prescribing
safety signs. This legislation was adapted
from the previously used BS 5499 to provide
standardised signage for all European Union
member states and remains the standard
used in the UK.
While the regulations state that only ISO
7010 compliant fire safety signage should
be installed, currently BS 5499 signs do not
need to be immediately replaced. However,
to ensure consistency, BS 5499 signs cannot
be mixed with ISO 7010 compliant signage,
meaning that when existing signs are
replaced, all signage on the premises must
be updated to ISO 7010 versions.
There are five specific categories of safety
signage, each of which has specific ‘intrinsic
features’ such as the colour, shape and
design to aid recognition, especially in an
emergency. While the regulations allow
some variation in terms of the design, these
intrinsic features must be maintained.
as sports halls and stadiums, larger signs
should be used to mark fire exits and ensure
they can be seen easily.
It is also important to avoid using too
many di erent signs in an area as this
can lead to confusion and important
information or instructions being missed.
It is also advisable to remove signs when
they are no longer necessary, for example
if the hazard is no longer present, to avoid
presenting misleading information.
SUPPORT FROM SUPPLIERS
The task of ensuring that all the correct
and compliant signage is in place can be
di icult, especially for large and complex
sites or where a facilities manager is
responsible for multiple sites. Working with
an experienced and accredited signage
supplier has a number of benefits, including
peace of mind that all the signs supplied are
fully ISO 7010 compliant. Leading suppliers
will also be able to provide specific and
tailored guidance for the site or premises
in question to ensure all legal obligations
are met. This can include carrying out a
site survey to establish all the needs of the
business and o er professional advice on
the best options available.
Workplace signage has an important
role in ensuring a safer environment for
employees where the risk from a given
hazard cannot be completely eliminated
using other methods. However, ensuring
all the correct signage is used in the right
place across a business premises can be
complex. Therefore, engaging with an
experienced and reputable supplier,
who can provide valuable support in
assessing and fulfilling the needs of the
business, is essential.
Further information on the features of
particular signage can be found in guidance
documents from the HSE.
Prohibition signs – round with red
edging, a diagonal line and black
pictogram. These are used to prohibit
behaviour that would cause a hazard or
impact health and safety. For example,
‘No smoking’, ‘No access for unauthorised
persons’ or ‘Do not touch’.
Hazard/Warning signs – triangular with
yellow background, black edging and
a black pictogram. These are used to
alert people to a potential hazard or
danger, such as high voltage or dangerous
materials.
Mandatory signs – round with a white
pictogram on a blue background. These
are instructional signs, used to direct
behaviour to ensure safety. For example,
‘Eye protection must be worn’.
Fire equipment signs – rectangular or
square with a white pictogram on a red
background. These indicate the location
of fire flighting equipment.
Emergency escape or first-aid signs
- rectangular or square with a white
pictogram on a green background. These
signs provide information designed to
enhance safety by directing people to
emergency exits, assembly points and
first aid materials.
The design and placement of these signs
should be considered carefully to ensure
they are e ective. They should be placed
at an appropriate height, usually eye level,
taking into account any potential obstacles
that may impact the visibility. The viewing
distance should also be considered. For
example, in large open plan areas such