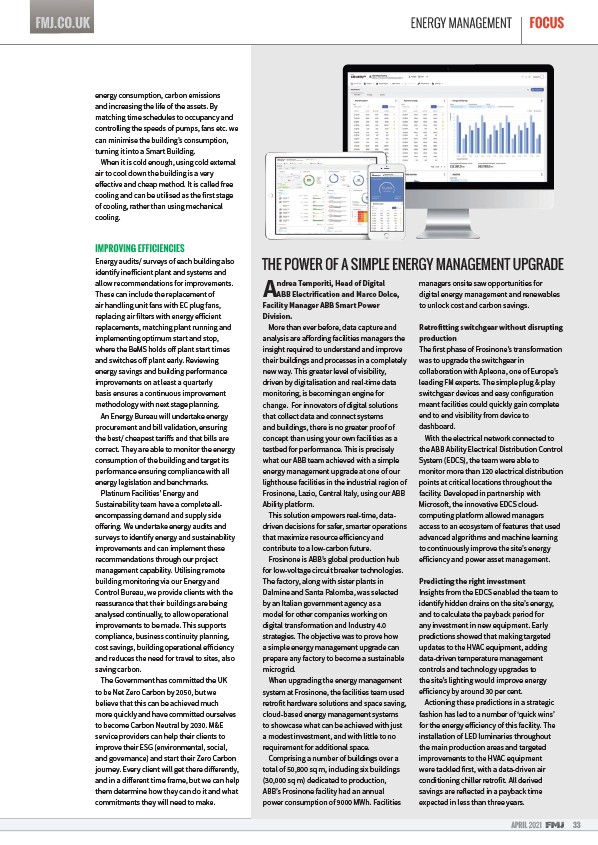
FMJ.CO.UK ENERGY MANAGEMENT FOCUS
THE POWER OF A SIMPLE ENERGY MANAGEMENT UPGRADE
APRIL 2021 33
energy consumption, carbon emissions
and increasing the life of the assets. By
matching time schedules to occupancy and
controlling the speeds of pumps, fans etc. we
can minimise the building’s consumption,
turning it into a Smart Building.
When it is cold enough, using cold external
air to cool down the building is a very
e ective and cheap method. It is called free
cooling and can be utilised as the first stage
of cooling, rather than using mechanical
cooling.
IMPROVING EFFICIENCIES
Energy audits/ surveys of each building also
identify ine icient plant and systems and
allow recommendations for improvements.
These can include the replacement of
air handling unit fans with EC plug fans,
replacing air filters with energy e icient
replacements, matching plant running and
implementing optimum start and stop,
where the BeMS holds o plant start times
and switches o plant early. Reviewing
energy savings and building performance
improvements on at least a quarterly
basis ensures a continuous improvement
methodology with next stage planning.
An Energy Bureau will undertake energy
procurement and bill validation, ensuring
the best/ cheapest tari s and that bills are
correct. They are able to monitor the energy
consumption of the building and target its
performance ensuring compliance with all
energy legislation and benchmarks.
Platinum Facilities’ Energy and
Sustainability team have a complete allencompassing
demand and supply side
o ering. We undertake energy audits and
surveys to identify energy and sustainability
improvements and can implement these
recommendations through our project
management capability. Utilising remote
building monitoring via our Energy and
Control Bureau, we provide clients with the
reassurance that their buildings are being
analysed continually, to allow operational
improvements to be made. This supports
compliance, business continuity planning,
cost savings, building operational e iciency
and reduces the need for travel to sites, also
saving carbon.
The Government has committed the UK
to be Net Zero Carbon by 2050, but we
believe that this can be achieved much
more quickly and have committed ourselves
to become Carbon Neutral by 2030. M&E
service providers can help their clients to
improve their ESG (environmental, social,
and governance) and start their Zero Carbon
journey. Every client will get there di erently,
and in a di erent time frame, but we can help
them determine how they can do it and what
commitments they will need to make.
Andrea Temporiti, Head of Digital
ABB Electrification and Marco Dolce,
Facility Manager ABB Smart Power
Division.
More than ever before, data capture and
analysis are a ording facilities managers the
insight required to understand and improve
their buildings and processes in a completely
new way. This greater level of visibility,
driven by digitalisation and real-time data
monitoring, is becoming an engine for
change. For innovators of digital solutions
that collect data and connect systems
and buildings, there is no greater proof of
concept than using your own facilities as a
testbed for performance. This is precisely
what our ABB team achieved with a simple
energy management upgrade at one of our
lighthouse facilities in the industrial region of
Frosinone, Lazio, Central Italy, using our ABB
Ability platform.
This solution empowers real-time, datadriven
decisions for safer, smarter operations
that maximize resource e iciency and
contribute to a low-carbon future.
Frosinone is ABB’s global production hub
for low-voltage circuit breaker technologies.
The factory, along with sister plants in
Dalmine and Santa Palomba, was selected
by an Italian government agency as a
model for other companies working on
digital transformation and Industry 4.0
strategies. The objective was to prove how
a simple energy management upgrade can
prepare any factory to become a sustainable
microgrid.
When upgrading the energy management
system at Frosinone, the facilities team used
retrofit hardware solutions and space saving,
cloud-based energy management systems
to showcase what can be achieved with just
a modest investment, and with little to no
requirement for additional space.
Comprising a number of buildings over a
total of 50,800 sq m, including six buildings
(30,000 sq m) dedicated to production,
ABB’s Frosinone facility had an annual
power consumption of 9000 MWh. Facilities
managers onsite saw opportunities for
digital energy management and renewables
to unlock cost and carbon savings.
Retrofitting switchgear without disrupting
production
The first phase of Frosinone’s transformation
was to upgrade the switchgear in
collaboration with Apleona, one of Europe’s
leading FM experts. The simple plug & play
switchgear devices and easy configuration
meant facilities could quickly gain complete
end to end visibility from device to
dashboard.
With the electrical network connected to
the ABB Ability Electrical Distribution Control
System (EDCS), the team were able to
monitor more than 120 electrical distribution
points at critical locations throughout the
facility. Developed in partnership with
Microso , the innovative EDCS cloudcomputing
platform allowed managers
access to an ecosystem of features that used
advanced algorithms and machine learning
to continuously improve the site’s energy
e iciency and power asset management.
Predicting the right investment
Insights from the EDCS enabled the team to
identify hidden drains on the site’s energy,
and to calculate the payback period for
any investment in new equipment. Early
predictions showed that making targeted
updates to the HVAC equipment, adding
data-driven temperature management
controls and technology upgrades to
the site’s lighting would improve energy
e iciency by around 30 per cent.
Actioning these predictions in a strategic
fashion has led to a number of ‘quick wins’
for the energy e iciency of this facility. The
installation of LED luminaries throughout
the main production areas and targeted
improvements to the HVAC equipment
were tackled first, with a data-driven air
conditioning chiller retrofit. All derived
savings are reflected in a payback time
expected in less than three years.