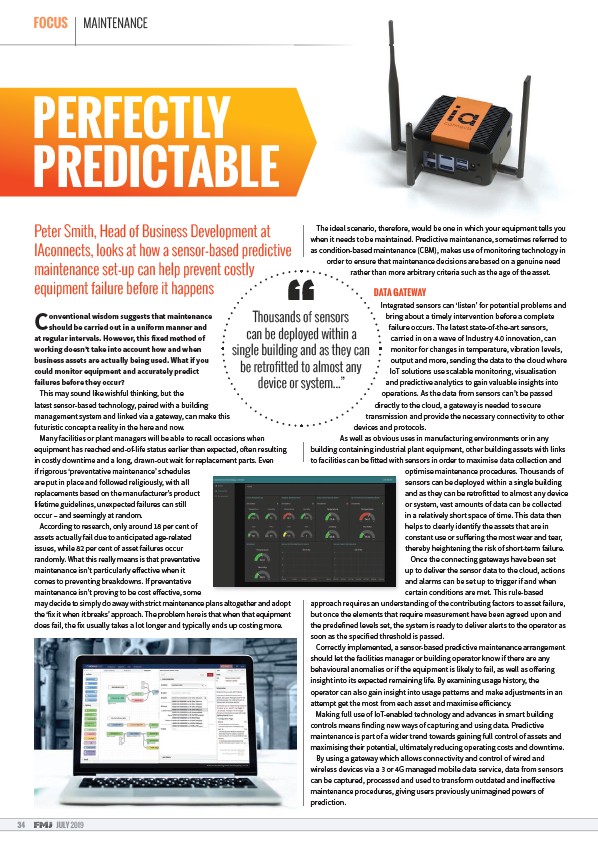
FOCUS MAINTENANCE
PERFECTLY
PREDICTABLE
Conventional wisdom suggests that maintenance
should be carried out in a uniform manner and
at regular intervals. However, this fixed method of
working doesn’t take into account how and when
business assets are actually being used. What if you
could monitor equipment and accurately predict
failures before they occur?
This may sound like wishful thinking, but the
latest sensor-based technology, paired with a building
management system and linked via a gateway, can make this
futuristic concept a reality in the here and now.
Many facilities or plant managers will be able to recall occasions when
equipment has reached end-of-life status earlier than expected, o en resulting
in costly downtime and a long, drawn-out wait for replacement parts. Even
if rigorous ‘preventative maintenance’ schedules
are put in place and followed religiously, with all
replacements based on the manufacturer’s product
lifetime guidelines, unexpected failures can still
occur – and seemingly at random.
According to research, only around 18 per cent of
assets actually fail due to anticipated age-related
issues, while 82 per cent of asset failures occur
randomly. What this really means is that preventative
maintenance isn’t particularly e ective when it
comes to preventing breakdowns. If preventative
maintenance isn’t proving to be cost e ective, some
may decide to simply do away with strict maintenance plans altogether and adopt
the ‘fix it when it breaks’ approach. The problem here is that when that equipment
does fail, the fix usually takes a lot longer and typically ends up costing more.
34 JULY 2019
The ideal scenario, therefore, would be one in which your equipment tells you
when it needs to be maintained. Predictive maintenance, sometimes referred to
as condition-based maintenance (CBM), makes use of monitoring technology in
order to ensure that maintenance decisions are based on a genuine need
rather than more arbitrary criteria such as the age of the asset.
DATA GATEWAY
Integrated sensors can ‘listen’ for potential problems and
bring about a timely intervention before a complete
failure occurs. The latest state-of-the-art sensors,
carried in on a wave of Industry 4.0 innovation, can
monitor for changes in temperature, vibration levels,
output and more, sending the data to the cloud where
IoT solutions use scalable monitoring, visualisation
and predictive analytics to gain valuable insights into
operations. As the data from sensors can’t be passed
directly to the cloud, a gateway is needed to secure
transmission and provide the necessary connectivity to other
devices and protocols.
As well as obvious uses in manufacturing environments or in any
building containing industrial plant equipment, other building assets with links
to facilities can be fitted with sensors in order to maximise data collection and
optimise maintenance procedures. Thousands of
sensors can be deployed within a single building
and as they can be retrofitted to almost any device
or system, vast amounts of data can be collected
in a relatively short space of time. This data then
helps to clearly identify the assets that are in
constant use or su ering the most wear and tear,
thereby heightening the risk of short-term failure.
Once the connecting gateways have been set
up to deliver the sensor data to the cloud, actions
and alarms can be set up to trigger if and when
certain conditions are met. This rule-based
approach requires an understanding of the contributing factors to asset failure,
but once the elements that require measurement have been agreed upon and
the predefined levels set, the system is ready to deliver alerts to the operator as
soon as the specified threshold is passed.
Correctly implemented, a sensor-based predictive maintenance arrangement
should let the facilities manager or building operator know if there are any
behavioural anomalies or if the equipment is likely to fail, as well as o ering
insight into its expected remaining life. By examining usage history, the
operator can also gain insight into usage patterns and make adjustments in an
attempt get the most from each asset and maximise e iciency.
Making full use of IoT-enabled technology and advances in smart building
controls means finding new ways of capturing and using data. Predictive
maintenance is part of a wider trend towards gaining full control of assets and
maximising their potential, ultimately reducing operating costs and downtime.
By using a gateway which allows connectivity and control of wired and
wireless devices via a 3 or 4G managed mobile data service, data from sensors
can be captured, processed and used to transform outdated and ine ective
maintenance procedures, giving users previously unimagined powers of
prediction.
Peter Smith, Head of Business Development at
IAconnects, looks at how a sensor-based predictive
maintenance set-up can help prevent costly
equipment failure before it happens
Thousands of sensors
can be deployed within a
single building and as they can
be retrofi tted to almost any
device or system...”