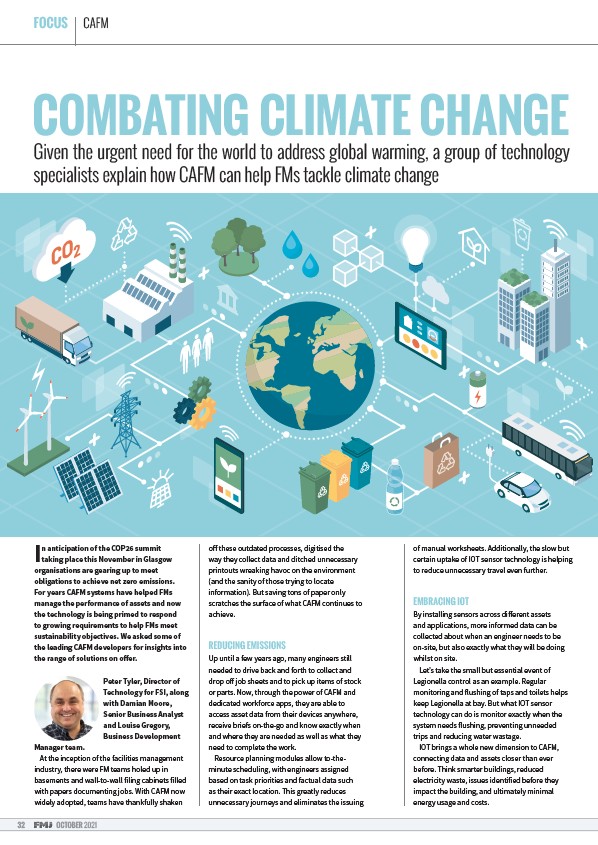
FOCUS CAFM
COMBATING CLIMATE CHANGE
Given the urgent need for the world to address global warming, a group of technology
specialists explain how CAFM can help FMs tackle climate change
In anticipation of the COP26 summit
taking place this November in Glasgow
organisations are gearing up to meet
obligations to achieve net zero emissions.
For years CAFM systems have helped FMs
manage the performance of assets and now
the technology is being primed to respond
to growing requirements to help FMs meet
sustainability objectives. We asked some of
the leading CAFM developers for insights into
the range of solutions on o er.
32 OCTOBER 2021
Peter Tyler, Director of
Technology for FSI, along
with Damian Moore,
Senior Business Analyst
and Louise Gregory,
Business Development
Manager team.
At the inception of the facilities management
industry, there were FM teams holed up in
basements and wall-to-wall filing cabinets filled
with papers documenting jobs. With CAFM now
widely adopted, teams have thankfully shaken
o these outdated processes, digitised the
way they collect data and ditched unnecessary
printouts wreaking havoc on the environment
(and the sanity of those trying to locate
information). But saving tons of paper only
scratches the surface of what CAFM continues to
achieve.
REDUCING EMISSIONS
Up until a few years ago, many engineers still
needed to drive back and forth to collect and
drop o job sheets and to pick up items of stock
or parts. Now, through the power of CAFM and
dedicated workforce apps, they are able to
access asset data from their devices anywhere,
receive briefs on-the-go and know exactly when
and where they are needed as well as what they
need to complete the work.
Resource planning modules allow to-theminute
scheduling, with engineers assigned
based on task priorities and factual data such
as their exact location. This greatly reduces
unnecessary journeys and eliminates the issuing
of manual worksheets. Additionally, the slow but
certain uptake of IOT sensor technology is helping
to reduce unnecessary travel even further.
EMBRACING IOT
By installing sensors across di erent assets
and applications, more informed data can be
collected about when an engineer needs to be
on-site, but also exactly what they will be doing
whilst on site.
Let’s take the small but essential event of
Legionella control as an example. Regular
monitoring and flushing of taps and toilets helps
keep Legionella at bay. But what IOT sensor
technology can do is monitor exactly when the
system needs flushing, preventing unneeded
trips and reducing water wastage.
IOT brings a whole new dimension to CAFM,
connecting data and assets closer than ever
before. Think smarter buildings, reduced
electricity waste, issues identified before they
impact the building, and ultimately minimal
energy usage and costs.