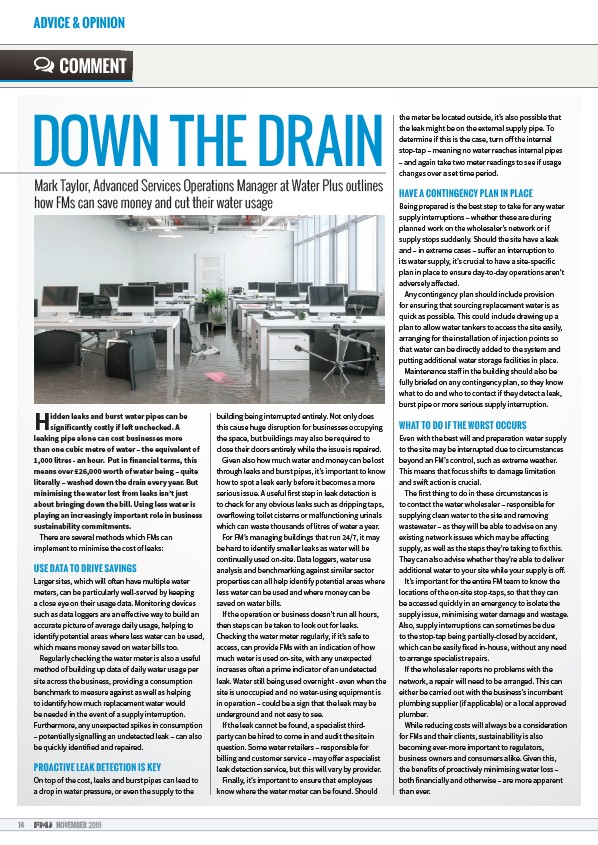
ADVICE & OPINION
COMMENT
DOWN THE DRAIN
Hidden leaks and burst water pipes can be
significantly costly if le unchecked. A
leaking pipe alone can cost businesses more
than one cubic metre of water – the equivalent of
1,000 litres - an hour. Put in financial terms, this
means over £26,000 worth of water being – quite
literally – washed down the drain every year. But
minimising the water lost from leaks isn’t just
about bringing down the bill. Using less water is
playing an increasingly important role in business
sustainability commitments.
There are several methods which FMs can
implement to minimise the cost of leaks:
USE DATA TO DRIVE SAVINGS
Larger sites, which will o en have multiple water
meters, can be particularly well-served by keeping
a close eye on their usage data. Monitoring devices
such as data loggers are an e ective way to build an
accurate picture of average daily usage, helping to
identify potential areas where less water can be used,
which means money saved on water bills too.
Regularly checking the water meter is also a useful
method of building up data of daily water usage per
site across the business, providing a consumption
benchmark to measure against as well as helping
to identify how much replacement water would
be needed in the event of a supply interruption.
Furthermore, any unexpected spikes in consumption
– potentially signalling an undetected leak – can also
be quickly identified and repaired.
PROACTIVE LEAK DETECTION IS KEY
On top of the cost, leaks and burst pipes can lead to
a drop in water pressure, or even the supply to the
14 NOVEMBER 2019
building being interrupted entirely. Not only does
this cause huge disruption for businesses occupying
the space, but buildings may also be required to
close their doors entirely while the issue is repaired.
Given also how much water and money can be lost
through leaks and burst pipes, it’s important to know
how to spot a leak early before it becomes a more
serious issue. A useful first step in leak detection is
to check for any obvious leaks such as dripping taps,
overflowing toilet cisterns or malfunctioning urinals
which can waste thousands of litres of water a year.
For FM’s managing buildings that run 24/7, it may
be hard to identify smaller leaks as water will be
continually used on-site. Data loggers, water use
analysis and benchmarking against similar sector
properties can all help identify potential areas where
less water can be used and where money can be
saved on water bills.
If the operation or business doesn’t run all hours,
then steps can be taken to look out for leaks.
Checking the water meter regularly, if it’s safe to
access, can provide FMs with an indication of how
much water is used on-site, with any unexpected
increases o en a prime indicator of an undetected
leak. Water still being used overnight - even when the
site is unoccupied and no water-using equipment is
in operation – could be a sign that the leak may be
underground and not easy to see.
If the leak cannot be found, a specialist thirdparty
can be hired to come in and audit the site in
question. Some water retailers – responsible for
billing and customer service – may o er a specialist
leak detection service, but this will vary by provider.
Finally, it’s important to ensure that employees
know where the water meter can be found. Should
the meter be located outside, it’s also possible that
the leak might be on the external supply pipe. To
determine if this is the case, turn o the internal
stop-tap – meaning no water reaches internal pipes
– and again take two meter readings to see if usage
changes over a set time period.
HAVE A CONTINGENCY PLAN IN PLACE
Being prepared is the best step to take for any water
supply interruptions – whether these are during
planned work on the wholesaler’s network or if
supply stops suddenly. Should the site have a leak
and – in extreme cases – su er an interruption to
its water supply, it’s crucial to have a site-specific
plan in place to ensure day-to-day operations aren’t
adversely a ected.
Any contingency plan should include provision
for ensuring that sourcing replacement water is as
quick as possible. This could include drawing up a
plan to allow water tankers to access the site easily,
arranging for the installation of injection points so
that water can be directly added to the system and
putting additional water storage facilities in place.
Maintenance sta in the building should also be
fully briefed on any contingency plan, so they know
what to do and who to contact if they detect a leak,
burst pipe or more serious supply interruption.
WHAT TO DO IF THE WORST OCCURS
Even with the best will and preparation water supply
to the site may be interrupted due to circumstances
beyond an FM’s control, such as extreme weather.
This means that focus shi s to damage limitation
and swi action is crucial.
The first thing to do in these circumstances is
to contact the water wholesaler – responsible for
supplying clean water to the site and removing
wastewater – as they will be able to advise on any
existing network issues which may be a ecting
supply, as well as the steps they’re taking to fix this.
They can also advise whether they’re able to deliver
additional water to your site while your supply is o .
It’s important for the entire FM team to know the
locations of the on-site stop-taps, so that they can
be accessed quickly in an emergency to isolate the
supply issue, minimising water damage and wastage.
Also, supply interruptions can sometimes be due
to the stop-tap being partially-closed by accident,
which can be easily fixed in-house, without any need
to arrange specialist repairs.
If the wholesaler reports no problems with the
network, a repair will need to be arranged. This can
either be carried out with the business’s incumbent
plumbing supplier (if applicable) or a local approved
plumber.
While reducing costs will always be a consideration
for FMs and their clients, sustainability is also
becoming ever-more important to regulators,
business owners and consumers alike. Given this,
the benefits of proactively minimising water loss –
both financially and otherwise – are more apparent
than ever.
Mark Taylor, Advanced Services Operations Manager at Water Plus outlines
how FMs can save money and cut their water usage